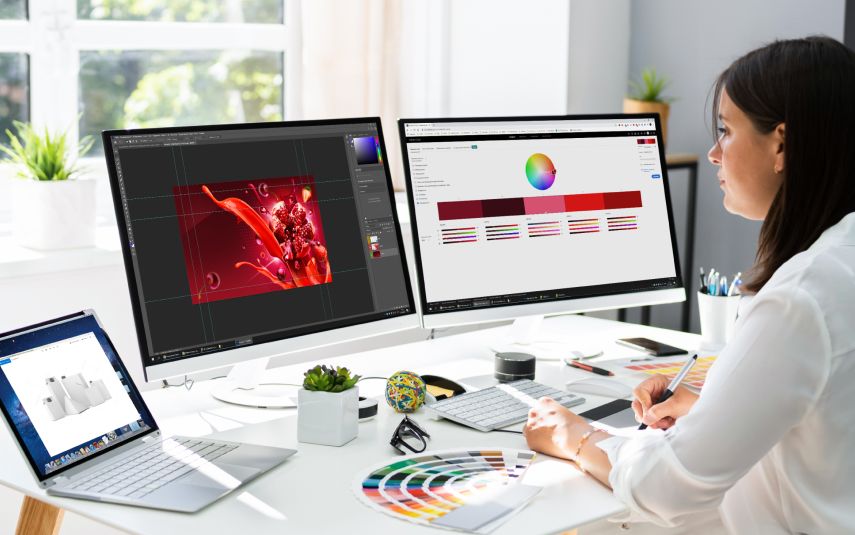
Invest in design
One of the sustainable trends today can be attributed to our consumers' involvement of advertising and marketing agencies, as well as specialized design studios for the systematic formation of the visual image of packaging. This process, as a rule, is accompanied by market research, assessment of consumer preferences, taking into account the requirements of the distribution network and has a pronounced marketing character.
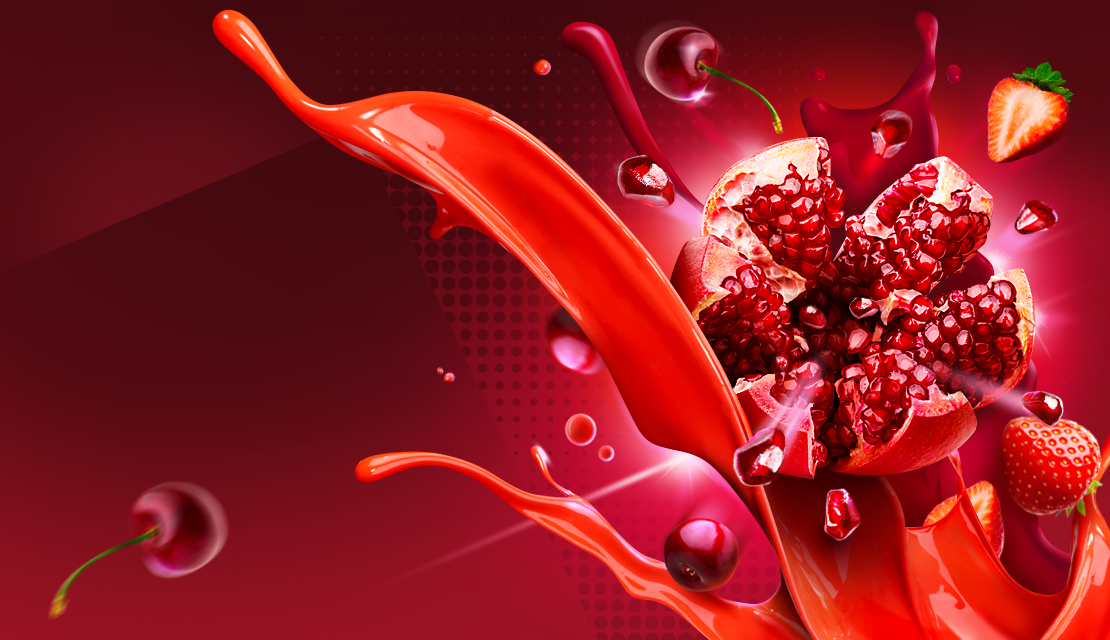
Design + Technology = Result
The main competencies of the prepress department of our printing house are focused today primarily on the technological aspect, namely in the qualified prepress preparation of the design and its adaptation to the required type of printed material. High-quality design, combined with qualified prepress preparation, allows to obtain finished packaging with maximum aesthetic and economic effect.